摩擦颗粒料在现代摩擦材料中广泛运用,它对改善摩擦材料的摩擦磨损性能,如制动效能,衰退,噪音等都有非常重要的作用,本文作者通过对有摩擦颗粒的摩擦材料的测试,结果表明,摩擦颗粒料是改善摩擦材料的性能的一种可行的方法之一。
随着汽车工业的迅速发展,对车辆的安全性和舒适性的要求越来越高。摩擦材料对车辆的安全性和舒适性有非常大的影响,特别强调摩擦材料要具有稳定的摩擦系数,其中包括摩擦系数对压力的稳定性,盘式刹车片在制动时压力可高达到50Mpa。摩擦系数对速度的稳定性,其制动速度高达225公里/小时。摩擦系数对温度的稳定性,由于频繁的连续制动,其刹车鼓表面恒定温度高达700度。许多大的摩擦材料公司都用台架试验制动时刹车鼓变为红色的图片作为其技术水平高的象征。以宣传其刹车片高温时的制动性能。由于这样的工况,对摩擦材料的摩擦性能提出了非常高的要求。由于车辆的增加,车辆的噪音严重污染环境,高速制动时的摩擦稳定性和震动对安全也有非常重要的影响。摩擦颗粒在现代摩擦材料中为改善摩擦材料的上述性能起到了非常重要的作用。十多年来,摩擦颗粒中的使用迅速发展。可谓异军突起。几乎欧美等各国的摩擦材料制造商都广泛使用。特别是欧洲比较著名的大公司,在负荷较重的盘式刹车片中都有加入不同的摩擦颗粒。
一、基本工艺:
摩擦颗粒基本组分可以根据需要而不同,一般含有粘合剂如液体树脂,橡胶或其他有机粘 图1 摩擦颗粒的图片 合剂,高炭材料,如石墨,焦碳等,摩擦调整剂,纤维等。经过混合,造粒,干燥等工艺制成。见图1。
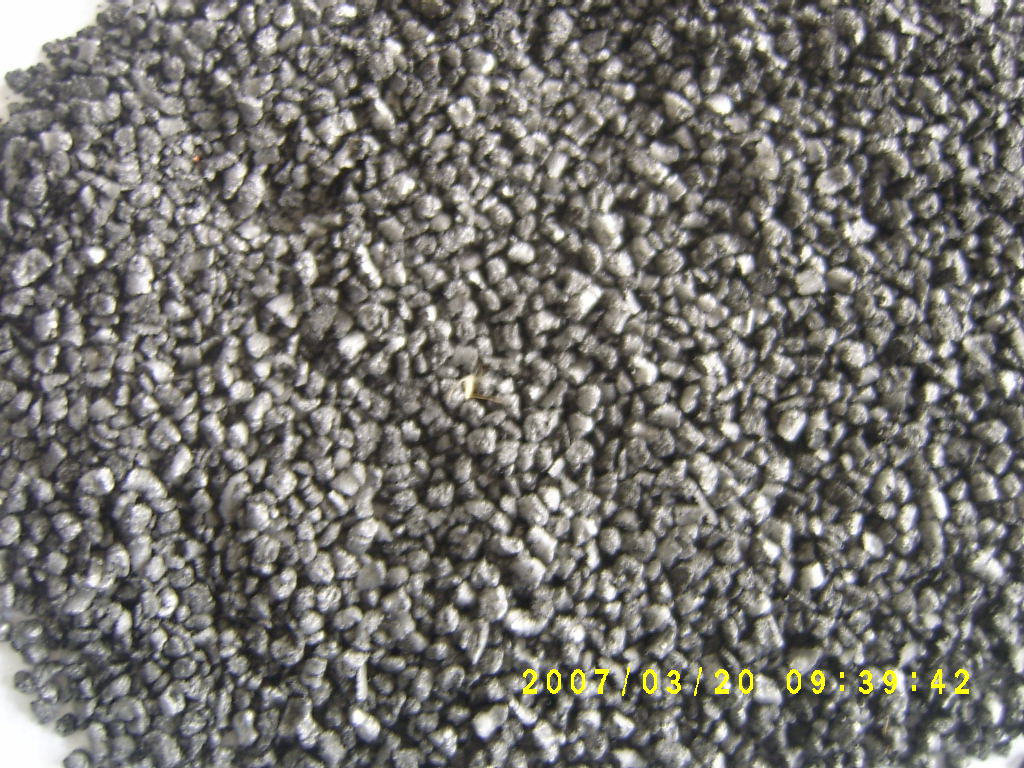
试验用具有代表性的含有摩擦颗粒的盘式刹车片基本配比如下:
各种纤维 10-30%,
润滑剂和填料 10–50%,
粘合剂 5-10%
摩擦颗粒 5-20%
其他摩擦性能调整剂和填料 适量
2:基本工艺:混料—压制—-热处理
二:试验方法和结果:
1:按照国标GB5763-1998
汽车用制动器衬片的试验方法,测试其摩擦系数和单位功的体积磨损率10-7cm3/Nm,同时还测试了每一个温度条件下的重量磨损(克)和根据重量磨损的重量计算的体积折算磨损率10-7cm3/Nm。和由重量磨损折算的体积磨损率的比较评估。重量磨损折算体积磨损率由下式计算 △V2=((△WH265)/(Wμ125)
其中:△V2由每一个温度下的重量磨损折算的体积磨损率10-7cm3/Nm
△ W 每一个温度下的重量磨损 克
H 样品的平均厚度 毫米
μ 每一个试验温度的平均摩擦系数
,试验结果见图2
2、按照QC/T 564/1999轿车制动器台架试验方法举行台架试验和按照QC/T582-1999 J轿车制动器性能要求对试验结果进行评估。
试验结果见图3.
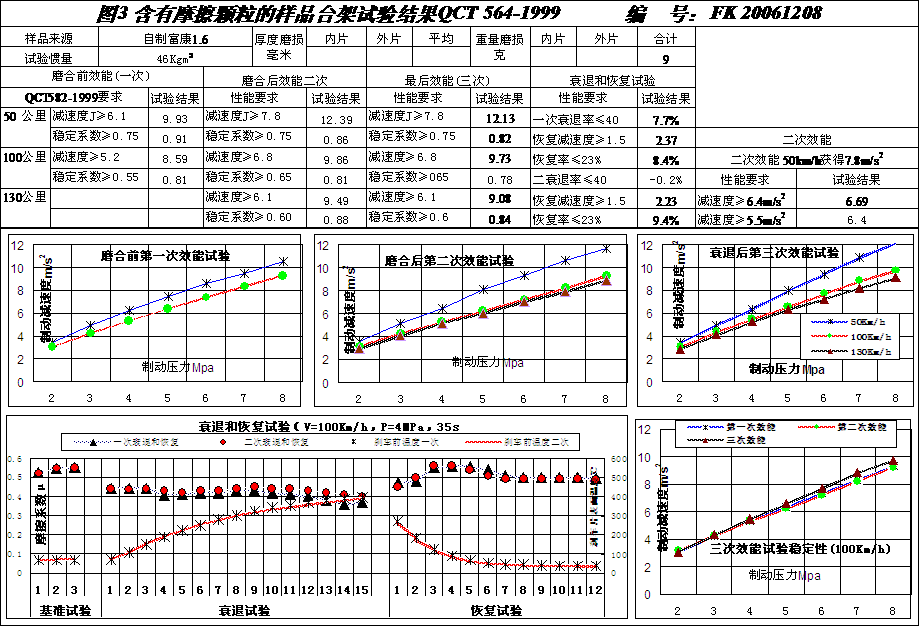
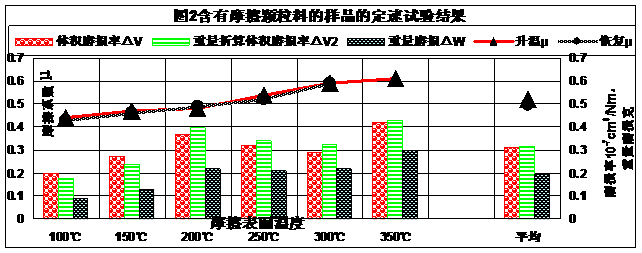
三、试验结果讨论:
从试验结果看,使用摩擦颗粒的盘式刹车片,无论是定速试验和台架试验,都有比较稳定的摩擦系数,台架试验中制动力矩稳定系数也比较好,衰退和恢复试验也比较好,特别是衰退试验,最低的摩擦系数接近0.4.,其恢复性能都比较稳定.由于摩擦颗粒的主要成分是炭,根据需要也要加入一些有机粘合剂,如弹性和韧性比较好的材料。试验结果表明,虽然加入了这一类材料,但在衰退试验中表现了良好的抗衰退性能。恢复性能也没有影响。
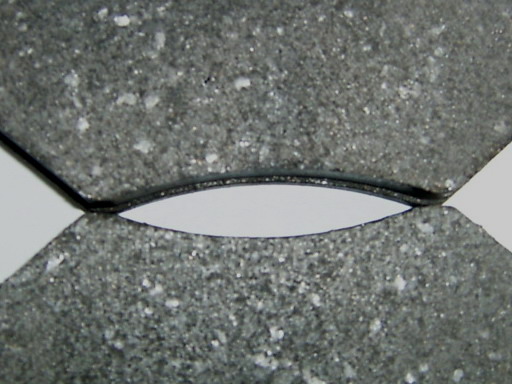
摩擦颗粒干燥时使用低温烘干,这样在树脂含量比较的的配方中比较容易和其他料结合,由于加入了一些纤维和使用造粒,可以避免颗粒料表面过于光滑。提高与其他材料的粘结能力,提高耐磨性。由于目前的这种摩擦颗粒是比较大的颗粒炭,可以减少由于炭含量太高而导致的制动效能降低,保证制动性能的稳定性。同时可以降低主体配方的粘结剂的用量。左面图4是用摩擦颗粒和特种纤维的复合材料的陶瓷型盘式刹车片的图片。
由于颗粒料的特殊工艺和一些特特殊的材料,如人造石墨,特种的润滑剂,摩擦控制添加剂等。其气孔率比一般的石墨颗粒高。高的气孔率对改善摩擦性能,
降低指导噪音是比较重要的。摩擦过程是一个非常复杂的物理化学过程光靠一种材料是不能解决的,因此配方的调适十分重要,如树脂含量,型号,纤维选择,润滑剂选择,工艺,干法或湿法,冷压,温压或热压。

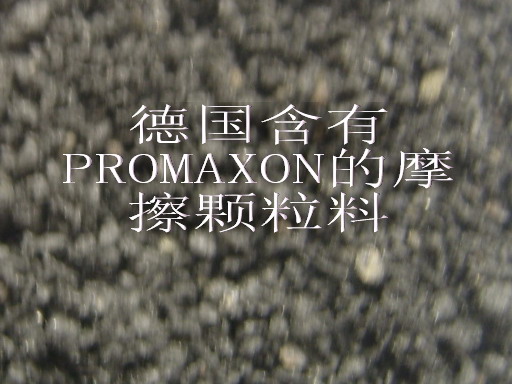
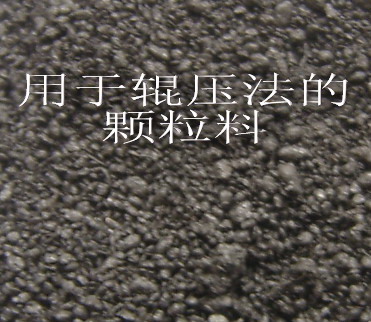
另外,可以根据客户的要求,制成各种不同特性要求的摩擦颗粒,如不同的颜色,不同的摩擦特性,如高摩擦的,低摩擦的,软质的硬质的纤维团的,橡胶基的树脂基的和各种无机和有机黏合剂的,不同的粒度等等。下面是几种摩擦颗粒的照片。
如德国的颗粒料,含有promaxon 等特别轻的填料,辊压法的颗粒料可以直接辊压成型或冷压成型。也可以作为予混料加入到其他料中复合,以改变混合料的工艺性能,如流动性,,弹性硬度等,钢纤维和炭等复合可以改变纤维方向,提高耐磨性,制动效能,噪音,克服半金属摩擦材料的部分缺点,以及降低成本,由于颗粒料可以自成体系,可以弥补主体配方的不足,起到相辅相成的作用。提高摩擦颗粒的含量可降低磨损,我们用20%的摩擦颗粒混合料的盘式刹车片按照SAEJ661a试验方法测试的摩擦性能如下:常温摩擦系数0.33,热摩擦系数0.32,摩擦级别EE级,重量磨损百分比1.09%,厚度磨损百分比0.96%。可见磨损是工艺降低的。
由于颗粒一般要用液体的黏合剂,因此混合的工艺和设备也需要进一步的试验研究。如混料机的选择,加料顺序和混合工艺方法,如何制造更好造颗粒的设备,干燥方法等。
以前,国内外有些工厂用密闭式炼胶机制造颗粒料,这种工艺设备投资费用比较高,如以前日本的α纤维,(一种含有橡胶和纤维的颗粒料),含有橡胶的粉碎料等,近几年来,由于混料机技术和原材料工业的发展,液体黏合剂的品种已有比较大的发展,如各种液体树脂,橡胶,以及无机和有机高分子材料。以及各种新的摩擦材料原料,使得比较容易的制成摩擦材料的颗粒料。这样可以用比较低成本和装备制造出合适的摩擦颗粒。
四、结论
- 摩擦颗粒料是改善摩擦材料的性能的一种可行的方法之一
- 对于颗粒的配方体系以及作用机理需要进一步的试验研究。
- 混合工艺和设备需要进一步研究和完善。
发表于《摩擦密封材料2007第3期》